Wednesday, May 31, 2006
Basic Blacksmithing Course Report
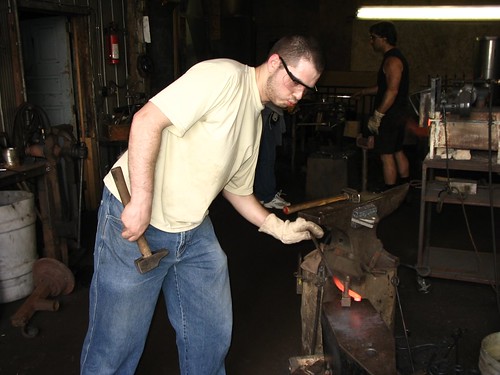
I’m not one to send money in the mail and I don’t like running things through the bank via cheques. So I spoke to Robb on the Thursday to find out if the course for the weekend was still running and if there was a spot available. Luckily yes it was and there was one spot available, so I told him I’d like to come and pay cash, which he said would be fine. And I accepted that if someone else wanted to pay first before I could pay, then well I would be out of luck. But that was not an issue at any rate.
The shop is about an hour and ten minutes drive away from where I live. Initially I believed the drive would take longer than this and had planned to sleep in my car overnight instead of driving back. There are accommodations in Elmira but I couldn’t justify even the least expensive bed+breakfast stay of $75 per night, so I packed a sleeping bag and a box of baby wipes instead.
The first session ran from 4:30PM to 8:30PM on Friday. Robb has 3 forges set up, two propane and one coal. The coal forge can achieve a greater heat and faster than the propane forges but is hotter to work around and requires constant attention to keep it going right. I worked on the coal forge the first day, and the propane forge on Saturday and Sunday. In this first session Robb taught us how to draw the steel out and make simple hooks and loops and points. This required much practice by me to get anything close to what Robb produced in his demonstrations. I also found my wrist to be very weak and it became difficult for me to keep my wrist straight while hammering after a while. Robb also demonstrated making the tongs that we would be working on the next day.
I’d planned to sleep in my car the first night, so after the day was done I cleaned up with baby wipes and set out for some McFood and a side order of reefer. After that I drove around and tried to find internet access, which I was successful at eventually. I was about to settle in for the night in the first location when a Police state authorized agent of gun wielding force slowly pulled up behind my parked car but then turned right. He probably didn’t know I was there but I didn’t want to be bothered by a cop not least of all when the interior of my car stinks like so much burnt flowers. So I drove back to the area of the McD’s where I could see so many secured wireless networks but no open ones, but decided to turn down a residential street (which is where I was able to find unsecured wireless in the other part of town where the cop buzzed me) and, surprisingly, I found a great connection within seconds of turning down that street. So I decided to stay there, and committed to passing out around 11. Things didn’t work out. By 12:40 I was still awake and uncomfortable as anything. I gave up and decided that an hour drive home would be worth it if I got some sleep because at the rate I was going I would see sunup with no shuteye. I’m glad I chose to go home as the rest was truly vital. I then decided that I’d just commute for the rest of the course, which I did without incident.
The second day was focused on completing the shovel that we made the handle of on the first day as part of the loops and drawing out exercises and beginning to make the pair of tongs. The shovel was interesting because we joined the handle to the scoop using rivets. The tongs were challenging and gave a good chance to build hammer precision striking experience because of the shape that was required for the finished product to function. I made 4 unsatisfactory attempts (heres two) before I had the techniques down well enough to pull it off, and the last 2 of the 6 total that I made were good enough with a bit of tweaking on my part. After Robb was satisfied with the two sides of our tongs, he demonstrated the power hammer to draw out the handles of our tongs. The power hammer is an amazing machine, it makes short work of drawing out hot steel. We also made hot and cold chisels plus a center punch out of recycled automotive suspension springs, a 5160 steel (carbon steel with a little chromium, very strong for high stress applications, as opposed to the 1020 steel, common carbon steel, that we used for the other projects). These striking tools were to be heat treated, the first stage of which was to slow cool them by plunging them hot into vermiculite, an insulator, and then leaving them there overnight.
The third day was spent finishing the chisels and punch, finishing the tongs, making a fire rake, and then a chance to play with some of the other techniques that Robb demonstrated such as upsetting, splitting and twisting. The heat treatment of the chisels and punch were completed by reheating them to a orange/yellow, then waiting for magnetism to return to the tips. As soon as magnetism was detected the tip was quenched. Then the scale (oxides) was pumiced off so the temper colors could be observed. As the yellowing color began to reach the tip, the tip was again quenched. The hardness of the tools was tested by using them and mine all stood up to a few initial uses. Time will tell how well they stand up in the future! Also, finishing the tongs was exciting because they are simple machine with moving parts and one that could be used in future work. It was very satisfying to be able to use them in handling hot work pieces later in the day. The two sides of the tongs were fitted together using a rivet and a striking mold to have the hammered side of the rivet take on the same shape as the rounded side. By the afternoon of the third day I was quite worn out and would have been happy to call it quits after finishing my chisels, punch and tongs, but I did want to complete my fire rake (top) (it doesn’t look so great) and at least do something with some of the other techniques. I ended up putting a plain twist on my bar-stock fire rake. I then put a slight squaring on a piece that I’d made of rod steel and put a twist on that section to show one of the twist patterns (one of the simplest hehe b/c the others are too much work!) that Robb demo’d. This piece is the one I am most proud of, possibly I will use it to hang a plant one day. I also made this strange thing on the third day. I wanted to come out with at least one thing that I could consider stabby or stabworthy. I used Robb’s high speed wire brush tools to clean up my work pieces and almost had one of them totally wrecked (I’d tried to use the big high speed wire brush to clean up the detailed hook end and the machine ate the workpiece and bent it to hell – fortunately it didn’t break the machine and I was also able to straighten it back out without too much trouble!). I then found out Robb has a smaller wire brush suitable for details that wont grab your work out of your hand haha.
All in all it was a long, tiring, dirty, sweaty, blistered and burned good time, and worth the money and long drives.
Link: Flickr Photo Stream (In here you’ll see all the pics, pics of Robb, a pic of me working hot steel, pics from around the shop, and pics of my work. Side note: Flickr always fucks up the order of the photos no matter what I seem to do, so I give up on it, too much hassle to try and deal with it!)
Comments:
Thanks all, I'm glad you enjoyed the post :) The heat treatment steps were recalled from memory, but I have a handout from the class that lists it all properly, if you'd like me to post that, please let me know.
Post a Comment
<< Home